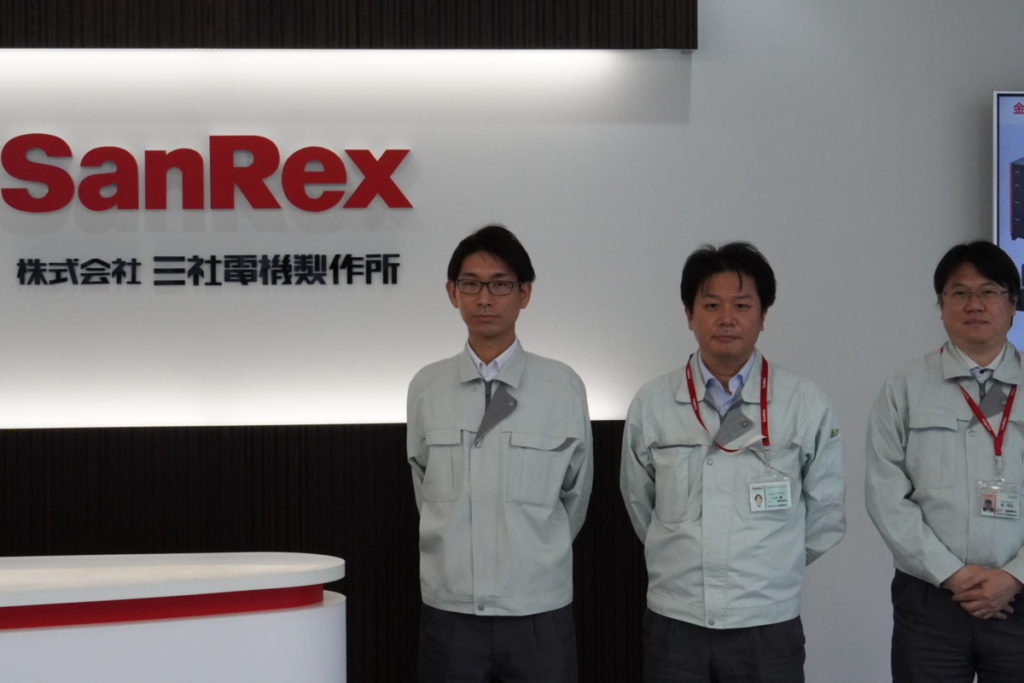
Typhoon HILユーザー事例(パワーコンディショナー)
株式会社三社電機製作所
山本 創様、伯 和雅様、三宅 剛洋様
- Typhoon HIL
- インタビュー
技術本部 開発第一部
(左から)三宅 剛洋様、山本 創様、伯 和雅様
完全自動化への取り組み
HILSを使い開発期間が大幅削減
-ご部署での業務内容を教えてください。
山本様:
各種エネルギー源を使ったパワーコンディショナーの開発、シミュレータ電源の開発を行っています。蓄電池や燃料電池、太陽光電池用が主な用途となっております。
-HILSというツールを知っていましたか。
山本様:
HILS(CHIL※1)は知りませんでしたが、PHIL※2というものは知っていました。PHILはユーザー様の現場で見せていただき知っていました。
※1 CHIL:Controller Hardware In the Loop
※2 PHIL:Power Hardware In the Loop
伯様:
HILSという言葉自体は以前から聞いてはいましたが、実際どんなものかはあまりよくは知らなかったですね。実際どのくらいのものか実機を見て初めて知りました。
三宅様:
私は全然知らなかったですね。今の部署に移ってきて初めて知りました。
-HILSを使おうと思ったきっかけを教えてください。
山本様:
HILS導入前は課題が2つありました。1つめは、デジタルの部分とパワー系の組み合わせ試験を行う前に、デジタルの試験が行える範囲が狭い。2つめは、ハード設計とソフト設計の仕事が並行して出来ずに、直列にしか仕事が出来ない。もちろん一部は並行して仕事が出来ましたが、ほとんどは直列で仕事を行っていました。
伯様:
HILS導入前は、回路シミュレータを使用して実際のソフトウェアのデバッグ作業を行っていました。回路シミュレータを利用する際にシミュレーションを実行し結果を確認する際には、相当な時間が発生する場合もあります。特に複雑なシミュレーションを行うと解析結果が得られるまでに長いと半日単位で時間がかかることがありました。
インタビューに受け答えする(左から)伯様、山本様
三宅様:
HILS導入前は実機が出来上がって、ソフトも出来上がっている状態でデバッグするのですが、実機では何かあったら壊れてしまいます。壊れたらまた作り直して、再度検証していました。改造をして、色々修正しながら進めていきますが、時間を要するところが課題でした。
インタビューに受け答えする三宅様
-Typhoon HILを選んだ理由を教えてください。
山本様:
1つめにCHILでそれなりの値段で買えるものが他に見当たらなかった。2つめにハードスペック的にみるとキャリア周波数が100kHzくらいであれば問題なくHILSとして動くと思えたのがきっかけでした。また自動車用のHILSはあったが、なかなか電力変換機用のHILSが見つからなかった。
私達に合うHILSが見つからなかったというのが正直な理由です。他のHILSを探したというよりは、Typhoon HILだとやりたいことが出来るということからほぼ一択に近かったという理由です。
-Typhoon HILをどのようなシステムでご利用していますか。
山本様:
パワーコンディショナーやPVと電池、あるいはFCと蓄電池がありますが、そういう全体的なシステムや変換器を繋いだ形や、系統安定化など新しい技術に対して有効活用しています。
三宅様:
系統安定化のパワーコンディショナーや、系統の電源側の電圧や周波数を変化させるようなことを行っています。今後は系統側の電圧、周波数が変化したときにパワーコンディショナーがどんな挙動を起こすのかということを検証していきたいと思っています。
評価対象のパワーコンディショナー(PCS)
-HILSを使って良かったところを教えてください。
山本様:
とにかく工程が短くなったのが一番大きいですね。また動作が目視的に見える。ソフトウェアとして正しいかどうかの判断がつきやすい。工場が滋賀に位置しているため、大型機器の確認のために大阪から滋賀まで何度も足を運ばせていたのですが、多くのことがこちらでも見えるようになり、メリットが大きいと感じております。今までは実機と組み合わせたソフトウェアの確認のため工場に出向き、逆に工場に行くとデバッグ環境が不足していました。
それがHILSを導入することで、ほとんど実験室でできて、あとは工場で動かすだけで済みます。工程はざっくりいえば30~40%は減りました。劇的に工数は変わったと思います。
インタビューに受け答えする山本様
伯様:
回路シミュレータを半日単位で解析していた内容が、HILSではリアルタイムに結果が反映されるのが非常に大きかったです。
また山本が話したように工場で実際に製品の最終的な確認を行っています。従来では、ハードエンジニアが動かしているのを横で見ながら、何か問題があったら、一つ一つログなどを解析しながら見ていく形で、実際に見えるところや、得られる情報は限られたりしています。
そんな中でソフト担当が現地でソフトを焼き直して確認するということを行っていましたが、その際に壊れてしまうこともありました。HILSがあればそういった作業を工場に行かなくても、状況だけ聞いて同じように再現して解析し、不具合等して再度確認して、ソフトをアップデートする。そういった形で、工場で行っている作業と並行して解析等をすすめられますので先ほどの大幅に短縮できたところの根本はその辺があるのかと思いますね。
また、パワーコンディショナーの系統連系試験は項目数が肥大化して大規格になっています。実際に現物で行うとなると時間も非常にかかり、人のリソースも設備的にも組み上げるのが大変です。私は今、Typhoon HIL Test IDEを活用して、系統連系試験を全て自動で行うということに取り組んでいます。これを行うと設備が不要で、夜間等に自動で試験実施を行い、翌朝確認ということができます。HILSでの試験内容が、そのまま認証が下りるかというと話はまた別ですが、不具合を無くすために全ての試験を行うということが非常に短時間で行えるようになりました。
山本様:
さきほどの話の通り、実機のデータを求められるものに関しては、もちろん試験を行うことは必須です。ただし、何か不具合があった時に「ソフトウェアは絶対に問題ない」ということをどのような形で担保するかだと考えています。少なくともHILSの中で正しく動けば、ハードに問題が無ければちゃんと動くというところにもっていけるということがあります。もう一つは、これから先の認証というものの中で実機と、あとはHILSで検証したものでいいよという話はあります。
評価基板とTyphoon HILの接続写真
-HILSを使って苦労している点を教えてください。
伯様:
動かしていて、日本語ドキュメントが少なかった点がちょっと苦労しました。最初のいくつかのドキュメントは、実際どういった仕組みになっているのかよく分かってないと、中々把握しづらかったりするので、そういった情報が日本語情報でもあるともうちょっと助かったかなとは思いました。英語のドキュメントでは細かいニュアンスが本当にあっているかも分からなかったりする場合もあるので、そういった点が日本語のドキュメントでないと確信を持てなかったということがありました。
三宅様:
MCなどたくさんの沢山素子を増やしていきたいときに、スペックの問題でそれ以上に増やせないというときに頭を悩ませました。HILSのFPGAのコンフィギュレーション※を変えれば使えるMCの数が増えますが、そうすると他のスペックが落ちてしまうので、バランスをどうするかというのは、すぐに結論が出ないので難しいという印象があります。
※コンフィギュレーションのテーブル設定にて、FPGAソルバーの構成比率を変更可能。(コア数やモータ数、MC数など)
-HILSを使って将来的にどのようなことを行いますか。
山本様:
既に対応し始めてはいますが、JETの系統連系試験に準ずる試験は大前提として全てHILSで行うことを考えています。2つめに、限界試験ですね。例えば、定格を超えた時にどんな動きをするのかプログラムで確認するのが必要かと思います。3つめに、もし出来るようであれば、フィードバック信号とかに高周波を注入して試験を行いたいです。
伯様:
私は、系統連系試験の自動化を今まさに行っている状況なので、これをどんどん広げていくことが一番大事かなと思います。またTyphoon HILはPythonで全て動かせるのも非常に大きいと思っています。最終的にはドキュメント作成や、そういったことまで全てPythonで制御して完全自動化できれば良いかなと思っています。ソフトを修正したら、自動でテストを実施する継続的インテグレーションの開発プロセスが出来れば良いなと思っています。
山本様、伯様、三宅様 ありがとうございました!
インタビュアー 杉山 潤、木山 浩伸、藤田 陽大、杉山 勇